Value Stream Mapping
Understanding and optimising value stream mapping (VSM)
What is value stream mapping?
Value stream mapping (VSM) is a tool for analysing and visualising production and business processes. It is used to record and visualise the entire flow of materials, information and resources from the idea to the end product. The aim of value stream mapping is to identify inefficient processes and develop measures for improvement and optimisation. It helps to recognise and eliminate waste, shorten throughput times and increase added value.
Value stream mapping is a powerful lean management tool that visualises the entire process chain of a product or service. It helps companies to understand the flow of materials and information in production and beyond, identify bottlenecks and eliminate waste. The entire process is analysed from start to finish, from the raw material to the finished product or from order acceptance to delivery. The analysis reveals potential for optimisation and increased efficiency - the aim is to make processes as lean and effective as possible, thereby reducing costs and shortening throughput times.
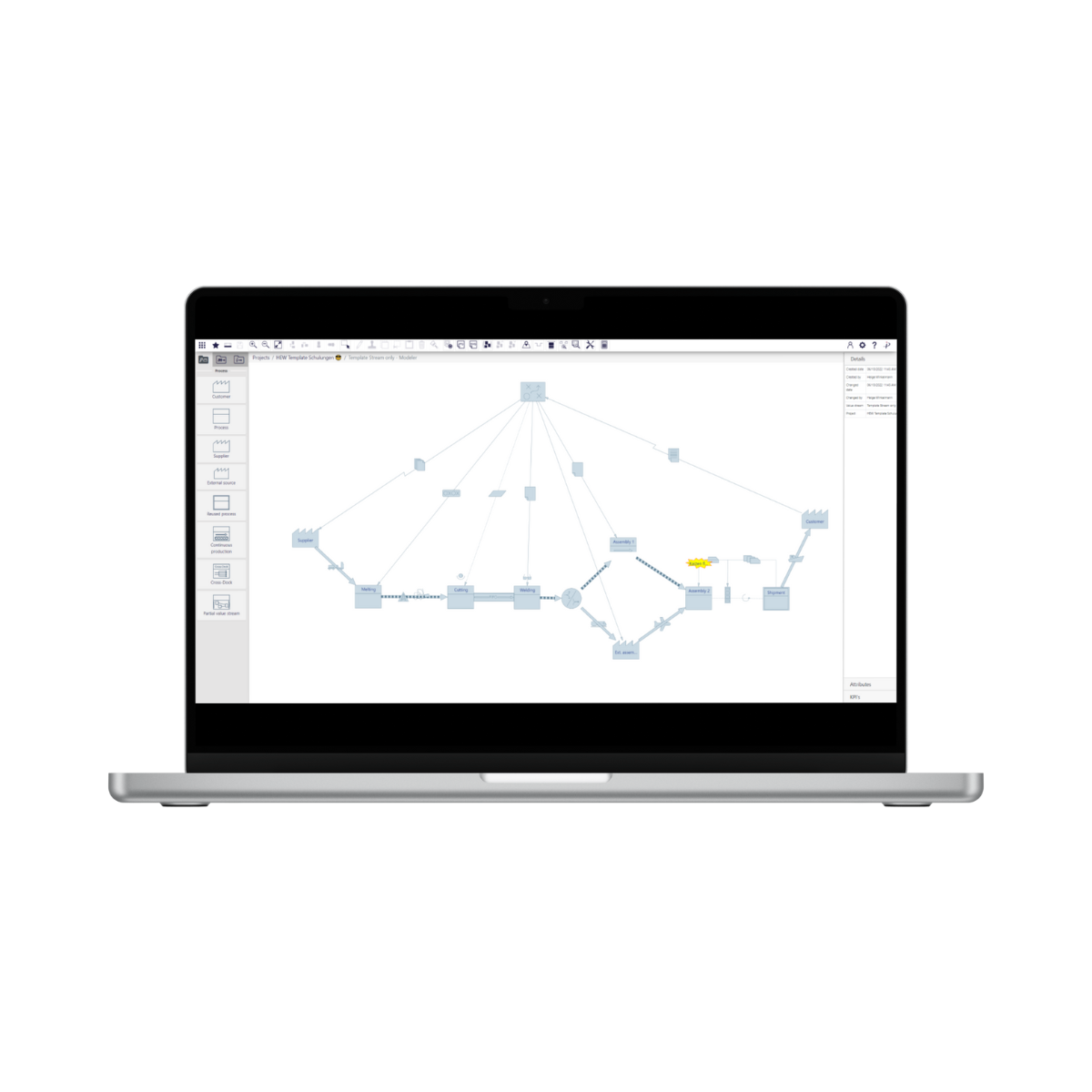
Why is value stream mapping important?
In many companies, processes and workflows often remain unclear and complex, which can lead to inefficient working methods and unnecessary waste. Value stream mapping offers a decisive advantage here by making all process steps visible and highlighting clear optimisation approaches. Companies can thus:
- Uncover waste - e.g. by minimising waiting times or duplication of work.
- Identify bottlenecks - and take targeted measures to eliminate them.
- Use resources efficiently - by optimising the flow of materials and information.
- Reduce costs and increase productivity - by eliminating non-value-adding activities.
Value stream mapping is therefore an indispensable tool for any company that wants to continuously improve and remain competitive.
Why value stream mapping is indispensable today
The basic principles of value stream mapping have not changed since its inception - they help to eliminate waste, optimise processes and unleash efficiency potential. However, with solutions such as Polaris, value stream mapping is now much more powerful and easier to implement. Thanks to digital transformation, analysing and optimising processes is becoming an ongoing, dynamic process that supports companies on their way to lean, agile production.
History of value stream mapping
Value stream mapping originally stems from the lean philosophy developed at Toyota in the 1950s. The concept was formulated by Taiichi Ohno, an engineer at Toyota, as part of the Toyota Production System (TPS). The aim was to reduce waste and make production more efficient. The idea of analysing the entire production process and differentiating between value creation and waste led to the development of value stream mapping as a specific tool.
In the 1990s, value stream mapping was further popularised by the publication of the book ‘Learning to See’ by Mike Rother and John Shook. It presented the tool as a central instrument of the lean methodology and explained how companies can optimise processes with the help of VSM.
Value stream mapping in the digital age
With digitalisation and the introduction of modern IT systems, value stream mapping has also evolved. Today, it is no longer just about manual process monitoring, but also about analysing large volumes of data in real time, simulations and automated optimisation. This is where Polaris comes in, which was specially developed to take value stream analysis to a new level.
VSM purpose and benefits
Value stream mapping has several purposes and benefits that make it a valuable tool for organisations:
- Process understanding: VSM helps to develop a deep understanding of existing processes by visualising all steps.
- Identification of waste: The main goal of VSM is to identify and eliminate waste. Waste can occur in various forms, such as overproduction, waiting times, unnecessary transport or errors.
- Reduce lead time: By analysing the entire flow of materials and information, bottlenecks and delays can be identified and eliminated.
- Increasing efficiency: VSM makes it possible to eliminate non-value-adding activities and optimise the use of resources.
- Improve communication: Visual mapping of processes promotes better communication and collaboration within the team.
Advantages of Polaris
Polaris offers specific advantages and functionalities that promote the purpose and benefits of value stream mapping (VSM), especially in modern manufacturing environments. Polaris is designed to maximise process efficiency, reduce waste and increase transparency in complex production systems. Here are the key purposes and benefits that value stream mapping through Polaris offers:
1. Automated and detailed visualisation
Polaris enables companies to visualise their production processes and value streams clearly and in detail. The intuitive user interface allows companies to precisely map and analyse complex production flows. The software automatically identifies all process steps, resource flows and intermediate storage locations in a production system so that the entire value stream is visualised. This helps decision-makers to quickly understand production processes and recognise weak points.
2. Rapid identification of waste
Polaris provides tools to accurately analyse process steps to identify non-value-adding activities and waste (e.g. waiting times, overproduction, unnecessary transport). By analysing production and warehouse data, the software helps to locate bottlenecks in real time, which is crucial for reducing lead times and realising efficiency potential. The software prioritises these bottlenecks and sources of waste according to their urgency and impact on productivity.
3. Simulation and optimisation
Polaris can be used to simulate and compare future production scenarios. This function is particularly valuable as companies can run through various ‘what-if’ scenarios before implementing changes in production. Polaris makes it possible to test alternative layouts, process modifications and resource adjustments and evaluate their impact on the entire value stream. This leads to informed decisions and reduces the risk of ineffective adjustments.
4. Increase efficiency
A key advantage of Polaris is its data-driven approach, which enables companies to make decisions based on precise, real-time data. Polaris analyses large amounts of data from different production areas and makes it available in a clear form, which speeds up decision-making processes and makes them more informed. This reduces time losses and promotes continuous process improvement.
5. Improved communication and collaboration
Polaris presents information in an easy-to-understand, visual form, which facilitates communication between different departments. Employees from different departments can understand the value stream mapping and work together on the same information basis. This promotes cross-team collaboration, strengthens employees' understanding of processes and makes it easier to identify potential for improvement.
6. Integration with production management tools
Polaris can be seamlessly integrated with other production management systems such as ERP and MES. This makes it possible to update data in real time and to monitor and control different aspects of the production process simultaneously. This integration capability facilitates a holistic view of production processes and the automation of data flows.
7. Continuous improvement and lean implementation
Polaris supports companies in the implementation of lean principles by providing the basis for continuous process optimisation. Through the repeated application of value stream mapping and the implementation of lean approaches, Polaris provides a solid foundation for continuous improvement (Kaizen) and helps companies to build a lean and flexible production in the long term.
8. Sustainability and resource conservation
By identifying inefficient processes and excessive consumption of resources, Polaris also contributes to sustainability in production. Optimised processes consume less energy, reduce waste and lower material consumption. This helps companies to work more sustainably and achieve cost efficiency at the same time.
Who is Polaris suitable for?
Polaris is ideal for companies that want to make their production process more efficient and transparent. It is particularly suitable for:
- Production companies with complex processes that want to improve transparency and efficiency.
- Logistics companies that want to optimise the flow of materials and avoid bottlenecks.
- Service sectors that want to improve their performance by analysing and optimising their process chains.
Polaris not only makes value stream mapping easier, but also more effective and comprehensive. This means that optimisation is not a one-off project, but a sustainable process that keeps companies competitive in the long term.
Reservations about VSM
Despite the many advantages that value stream mapping offers, there are also reservations:
- Complexity: creating a value stream can be complex and time-consuming, especially if the process involves many variables and participants.
- Resistance to change: Employees and managers may perceive change as a threat to their usual ways of working and resist change.
- Lack of expertise: Creating value stream diagrams requires specialised knowledge. Without sufficient training, companies may find it difficult to implement the analysis correctly.
- Costs: The implementation of VSM and the subsequent realisation of improvement measures can initially require resources and time.
In which areas is value stream mapping used?
Value stream mapping (VSM) is no longer limited to industrial production. Its method for optimising and streamlining processes has proven itself as a universal tool and is now used in a wide range of industries. Whether in production, services or public administration, VSM helps to make processes more efficient and optimise the use of resources. Thanks to modern software solutions such as Polaris, it is now easier than ever to analyse the value stream and implement sustainable improvements.
Production and manufacture
VSM optimises production processes, reduces waste and cuts throughput times in production.
Logistics and supply chain management
VSM improves the flow of goods, reduces inventories and optimises delivery times through precise process visualisation.
Healthcare system
VSM reduces waiting times, improves patient flow and optimises processes in hospitals and surgeries.
Service sector
VSM streamlines processes, increases customer satisfaction and visualises information flows in service companies.
IT and software development
VSM makes development processes more efficient, reduces waiting times and improves team collaboration in IT.
Research and development
VSM optimises development cycles, visualises processes and reduces costs in R&D departments.
Symbols in the value stream
Various symbols are used in value stream mapping to represent the individual process steps and information. The most common symbols include:
How to carry out a value stream analysis
Step by step
A value stream mapping involves several steps:
- Identify the process: Define the process you want to analyse from start to finish.
- Collect data: Gather information about the current state of the process, e.g. through interviews, observations and documentation.
- Map the process: Create a value stream diagram of the current process (current state).
- Identify waste: Analyse the diagram and look for waste (e.g. unnecessary waiting times or overproduction).
- Develop improvement options: Develop solutions to eliminate waste and improve flow.
- Define target state: Create a diagram of the future process (target state).
- Implement measures: Implement the improvements and monitor the results.
Important tips for VSM
- Involve all relevant stakeholders: Ensure that all stakeholders, including the employees carrying out the process, are involved in the analysis.
- Focus on the overall process: Don't just look at the details, but analyse the entire value stream.
- Create a clear as-is and to-be analysis: Clearly define what the current state is and what the future process should look like.
- Set clear goals: Set measurable goals for improving the process.
Polaris VSM - The value stream mapping of the future
Polaris digitally implements the decades-old principles of value stream mapping and offers companies of all sizes the opportunity to optimise their production flow precisely, flexibly and sustainably. The software combines the traditional efficiency improvement of lean methods with the advantages of digital real-time analysis, opening up completely new opportunities for companies to eliminate waste and maximise productivity.